Our Forging Offerings
Engage with the skilled forging professionals at Frigate, who not only recognize the distinct challenges and needs of your business but also bring a wealth of industry experience and insights to the table, ensuring tailored solutions that drive success.
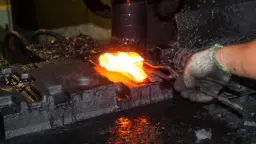
Open Die Forging
We specialize in open-die forging, a technique that employs flat dies to meticulously shape large components. This process enhances the material's properties through precise deformation, resulting in exceptional strength and durability.
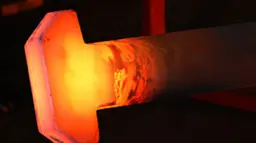
Upset Forging
We specialise in upset forging, producing high-strength components by deforming heated metal billets. This technique enhances material properties and ensures superior performance for intricate shapes in industrial applications.
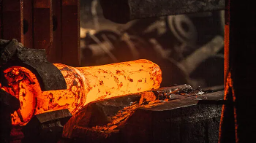
Closed Die Forging
Closed Die Forging ensures high precision in dimensions by restricting metal within meticulously engineered dies. This approach enhances the flow of grains, leading to increased strength and overall material integrity.
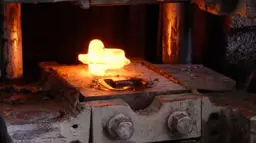
Drop Forging
The drop forging process employs rapid hammers to manipulate metal under regulated strain rates, ensuring enhanced mechanical properties and exact dimensional precision in intricate geometries.
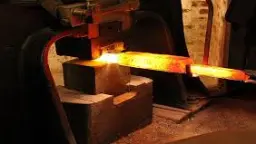
Precision Forging
Precision forging techniques that deliver exceptional dimensional accuracy and preserve material integrity. These processes are aimed at reducing waste and improving mechanical properties, resulting in top-notch components.
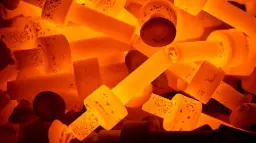
Net Shape Forging
We provide a Near-Net Shape Forgings service which significantly cuts down on material waste and lessens machining demands. It provides outstanding precision, enhanced mechanical properties, and remarkable structural integrity.
Custom Forging Solutions
KAMCO LLP is committed to excellence as a premier manufacturer, providing our clients with superior forged components. Our profound technical expertise ensures optimal microstructural integrity, extended product lifespan, enhanced strength, and reduced material waste, all while offering competitive pricing.
We specialize in the production of forged components tailored for high-demand service applications. Whether it involves small steel forgings for off-highway vehicles, defense, and agricultural equipment, or aerospace components utilizing high-temperature alloys, we possess the capability to fulfill a wide array of requirements with precision and reliability.
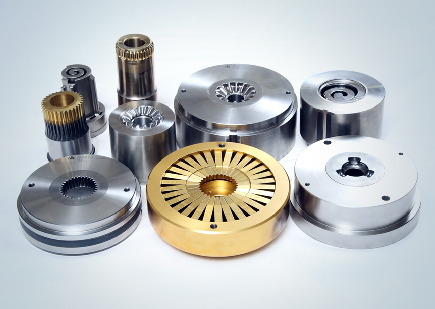
Industries We Serve
Aerospace
Agriculture
Automotive
Construction
Defence
Energy
Railroad
Oil & Gas
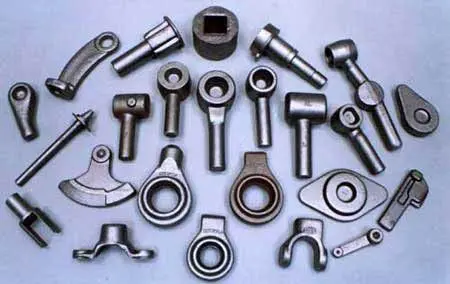
Our Forging Process
Custom dies are engineered with cutting-edge CAD/CAM software to achieve precise tolerances and manage complex shapes, guaranteeing consistent quality and reliability in manufacturing.
Forging machinery, like hydraulic or mechanical presses, delivers controlled, high-impact forces to shape the material while keeping its grain flow intact for improved strength.
The process aligns the material's grain structure with the part's shape, significantly enhancing directional strength and fatigue resistance.
Components are subjected to cooling in regulated environments to control thermal gradients, thereby reducing residual stresses and avoiding structural deformations.
Heat treatment methods, including annealing, quenching, and tempering, are employed to increase hardness, toughness, or wear resistance, specifically designed to suit the requirements of the application.
Material we use
Alloy Steel is created by heating and forging steel with elements like chromium, nickel, and vanadium, which improves its toughness, wear resistance, and corrosion resistance.
Aluminium is a lightweight metal that forges at lower temperatures, making it ideal for aerospace and automotive uses. It offers a strong strength-to-weight ratio and excellent corrosion resistance.
Brass, made from copper and zinc, is utilized for fittings, valves, and decorative items, valued for its workability and beauty.
Carbon steel is heated and shaped by hammering or pressing. Known for its strength, it is used in tools and structures, offering high durability and wear resistance.
Duplex steel, combining austenitic and ferritic stainless steels, is known for its high strength and corrosion resistance, making it ideal for chemical processing and offshore applications.
Copper serves a variety of purposes, including the creation of electrical devices, plumbing applications, and artistic items. Its processing requires careful oversight to minimize oxidation. This metal is recognized for its superior electrical conductivity, resistance to corrosion, and flexibility.
Stainless steel is known for its corrosion resistance and is commonly found in medical tools, food processing, and marine uses. It offers strength and an attractive look.
Titanium is crafted under exacting conditions to yield strong, lightweight elements for use in aerospace, medical implants, and high-performance fields. This material boasts a superior strength-to-weight ratio, exceptional corrosion resistance, and compatibility with living tissues.
Tool steel is used for making cutting tools, dies, and molds. It is known for its hardness, wear resistance, and ability to maintain a sharp edge.
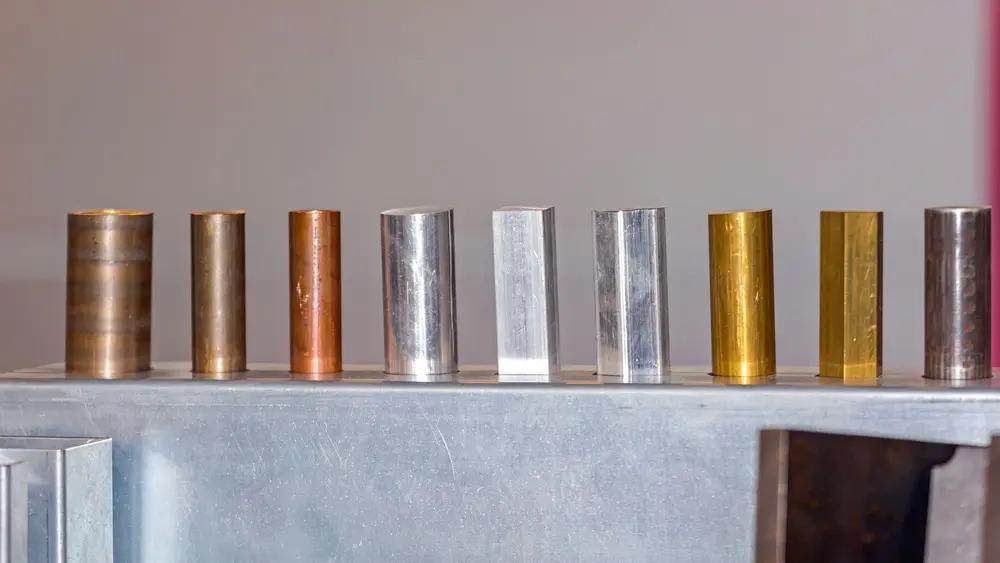
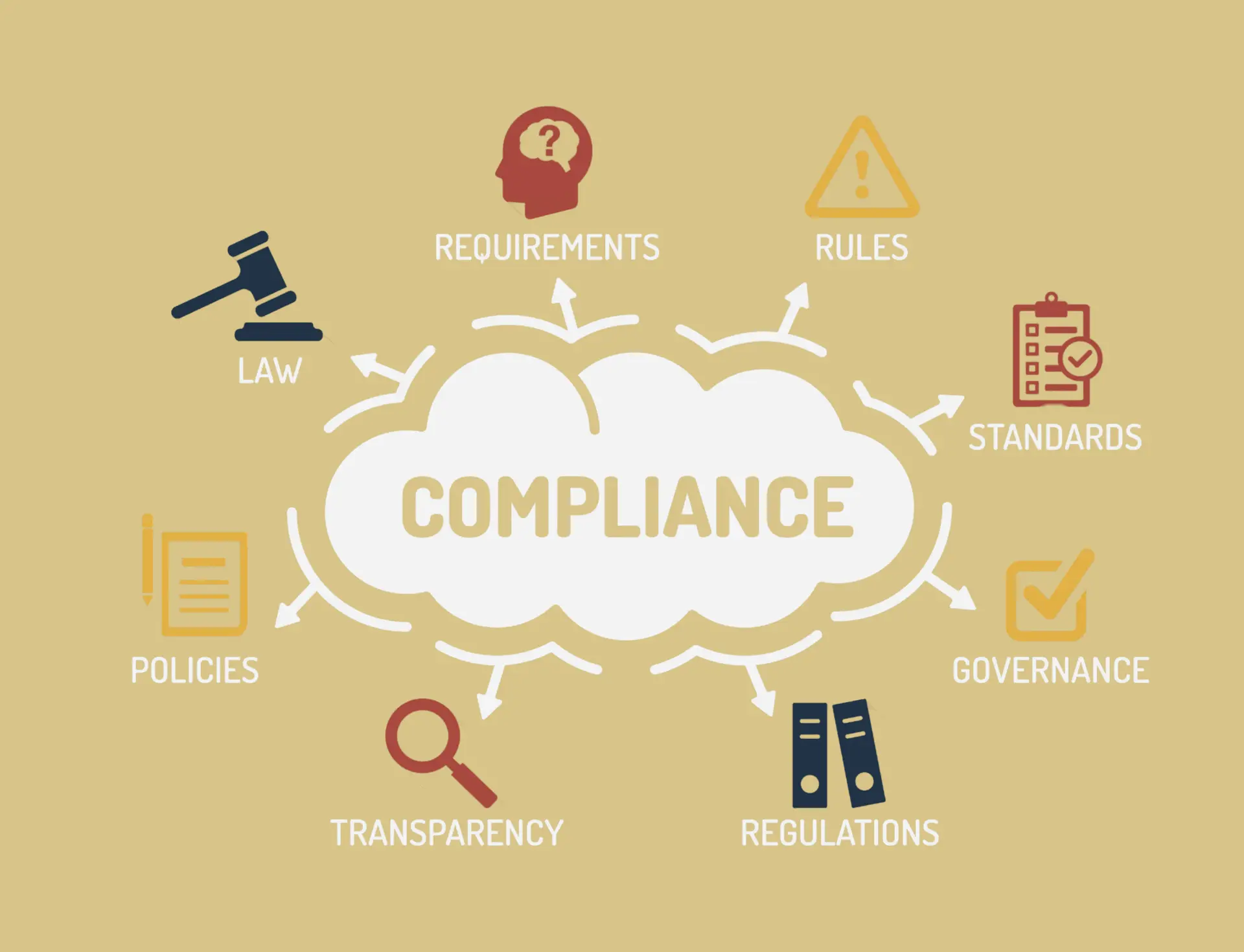
Meeting Global Standards
Specifies quality management protocols for aerospace applications, highlighting the need for meticulous control of material attributes, dimensional precision, and traceability in high-performance forged elements.
Details the technical criteria for steel forgings, focusing on chemical composition, mechanical attributes, non-destructive testing procedures, and the uniformity of grain structure.
Defines the technical criteria for quality management systems in automotive forging, highlighting the importance of process capability, defect prevention, and material compliance for components that are essential for safety.
Develops a coherent system for managing process control and traceability, ensuring consistent forging tolerances, reducing defects, and complying with customer specifications.
Defines guidelines for environmental management, ensuring that forging processes, including furnace emissions and waste treatment, adhere to worldwide sustainability standards while preserving metallurgical quality.
Confirms adherence to specialized methods such as heat treatment and surface enhancement, ensuring reliable metallurgical properties, hardness, and material performance for aerospace and defense forgings.
Monitors the safe operation of forging presses and machinery, implementing safety measures, conducting regular checks, and providing training for personnel to decrease the risk of accidents at work.
Controls the application of toxic substances in alloys and coatings, upholding material compliance for environmentally conscious uses.
Tolerances
±0.5 mm to ±3 mm
Varies by part size, die wear, and forging process (open or closed die).
0.25 mm per 100 mm of length
Determined by material flow and die precision during compression.
±0.5% of diameter
Critical for shafts and circular parts; adjusted for material properties.
1 mm per 100 mm of length
Influenced by cooling rate and die alignment.
Ra 3.2 to Ra 12.5 µm
Depends on die surface and material; secondary machining may improve it
±2% of target weight
Managed through strict material control and forging cavity filling.
±1°
Ensures proper geometry of inclined or angled surfaces.
±0.2 mm per 100 mm distance
Critical for ensuring functional fit of holes, slots, and keyways.
±5% of nominal thickness
Controlled by uniform material flow during the forging operation.
±0.2 mm to ±1 mm
Consistent with design specifications to prevent stress concentrations.
±0.1 mm to ±0.5 mm
Precision maintained for components requiring shafts or bearings.
±0.2 mm
Critical for preventing fatigue and ensuring smooth transitions.
3° to 5°
Required for easy removal of forged parts from dies; varies by geometry.
±0.05 mm to ±0.2 mm
Ensures alignment between internal and external features.
±0.1 mm per 100 mm distance
Maintains even spacing between parallel faces for load distribution.
±0.3 mm to ±1 mm
Tolerance for slots, grooves, and cavities.
±0.1% of dimensions
Considered for high-temperature forgings to manage post-cooling changes.
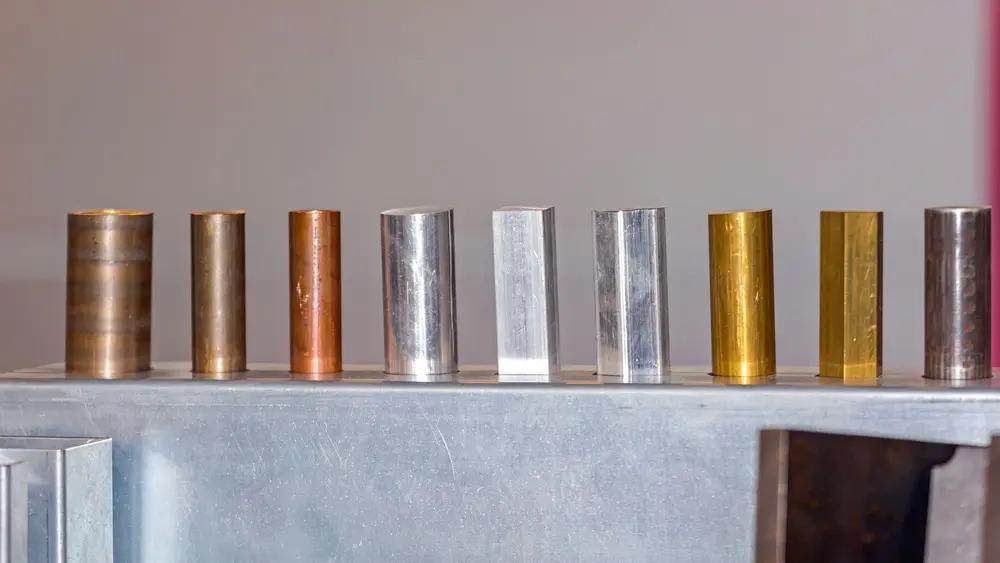